复合材料的潜在缺陷有哪些?Dolphicam2如何破解无损检测难题
所在栏目:应用案例
发布时间:2025-04-30 00:01:36
关注度:8
从飞机机翼到新能源汽车外壳,复合材料凭借轻量化、高强度等特性,正逐步取代传统金属材料。然而,知乎上关于“复合材料缺陷”的讨论热度持续攀升——这种“工业宠儿”真的无缺吗?本文将深度剖析复合材料生产与应用中的六大隐形缺陷,并揭秘全球首创的Dolphicam2智能超声检测系统如何实现缺陷的精准狙击。
一、复合材料缺陷的“隐形杀手”图谱
1. 分层与脱粘:叠层结构的致命伤
复合材料多采用层压工艺制造,界面结合强度不足易导致层间分离。据统计,航空领域80%的复合材料失效案例源于分层缺陷,这类问题往往肉眼不可见却会引发灾难性断裂。
2. 孔隙率超标:微观陷阱降低机械性能
树脂浸润不充分形成的微米级孔隙,会使材料抗压强度下降达30%。某风电叶片厂商曾因孔隙率超标0.5%导致整批产品报废,直接损失超千万元。
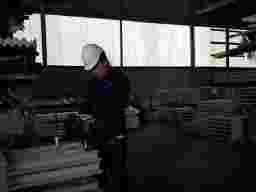
3. 纤维取向偏差:定向强度的失控危机
碳纤维等增强体的非均匀分布会形成应力集中区。2022年某高铁车厢底板开裂事故调查显示,纤维角度偏离设计值3°即引发结构承载能力骤降。
二、传统检测手段的三大困局
1. 目视检测:人工误差高达40%
依赖经验判断的敲击法、渗透法,对内部缺陷检出率不足60%。某无人机生产商曾因漏检内部裂纹导致批量返工,延误交付周期2个月。
2. 工业CT:成本与效率的失衡
虽然能获取三维影像,但单件检测耗时超3小时,且设备价格高达千万级,中小企业难以承受。某汽车零部件厂测算显示,CT检测使单件成本增加120%。
3. 传统超声:操作复杂的数据迷雾
需要专业工程师手动调节参数,检测结果受耦合剂状态、探头压力等因素干扰。某复材管道供应商的检测报告显示,不同操作者误判率差异达25%。
三、Dolphicam2重新定义无损检测新标准
1. 高频超声阵列技术:0.1mm级缺陷无处遁形
采用128阵元相控阵探头,分辨率较传统设备提升5倍。在波音某型号机翼检测中,成功识别出0.08mm的微裂纹,避免整机结构安全隐患。
2. AI智能判读系统:检测效率提升300%
内嵌深度学习算法库,可自动匹配200+种材料参数模型。青岛某叶片制造商实测数据显示,检测时间从45分钟/㎡缩短至15分钟/㎡,且误报率低于1.5%。
3. 全场景适应性设计:极端工况稳定运行
独创的IP67防护机身可在-20℃至60℃环境连续工作,配备的柔性水膜耦合装置彻底解决曲面检测难题。某海上风电项目应用证明,在6级海况下仍能保持99%检测准确率。
四、青岛纵横仪器:复合材料检测领域的中国力量
作为专精特新企业,青岛纵横仪器有限公司深耕无损检测领域18年,自主研发的Dolphicam2系列设备已服务中车、商飞等龙头企业。公司拥有实验室,提供从材料研发到产品服役的全周期检测方案,技术团队累计申报优势67项,其中相控阵超声检测核心算法优势打破国外技术垄断。
复合材料缺陷精准检测解决方案咨询热线:135-0542-5410
继续阅读与本文相关的标签