碳纤维缺陷结构与力学性能研究新突破,技术创新驱动材料革命
所在栏目:专业知识
发布时间:2025-04-26 11:37:04
关注度:19
在航空航天、新能源汽车、装备制造等领域,碳纤维复合材料因其高比强度、耐腐蚀性及轻量化特性,已成为不可替代的战略材料。然而,材料内部的微裂纹、孔隙、纤维错位等缺陷,往往成为制约其力学性能与安全性的关键瓶颈。近年来,随着无损检测技术的突破性进展,碳纤维缺陷结构的精准诊断与性能优化迎来全新机遇。
一、碳纤维缺陷类型及其对力学性能的影响
碳纤维复合材料的缺陷通常分为制造缺陷(如树脂分布不均、纤维束断裂)与服役损伤(如冲击分层、疲劳裂纹)。研究表明,孔隙率每增加1%,材料层间剪切强度可能下降5%-10%;而微裂纹的扩展则直接导致结构在循环载荷下发生脆性断裂。
在航空领域,碳纤维机翼蒙皮中的隐藏缺陷可能引发灾难性事故。因此,精准识别缺陷类型、定位缺陷位置并量化其影响,是提升材料可靠性的核心课题。
二、无损检测技术的革新:从理论到实践
传统检测手段如超声波扫描、X射线成像虽广泛应用,但存在分辨率不足、操作复杂等局限。近年来,多模态融合检测技术成为研究热点,结合红外热成像、激光散斑与声发射技术,可实现缺陷的三维可视化与动态监测。
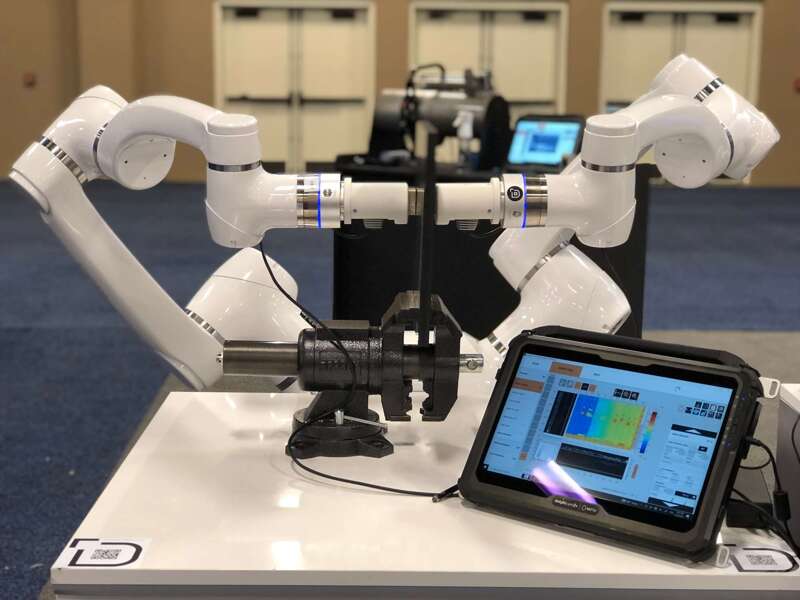
值得关注的是,Dolphicam2智能检测系统在这一领域的表现尤为突出。该系统采用高频涡流与深度学习算法,可精准识别直径小于0.1mm的微孔隙,检测效率较传统方法提升40%以上。其*非接触式设计*不仅避免了对材料的二次损伤,还支持复杂曲面构件的快速扫描,成为碳纤维质量控制的关键工具。
三、Dolphicam2的核心优势解析
高精度与高效率并存
Dolphicam2搭载的多频涡流探头,可同时捕捉表面与近表面缺陷信号,结合AI驱动的数据分析模块,实现实时成像与缺陷分类。实验数据显示,其对分层缺陷的检出率高达99.3%,误报率低于0.5%。
适应性强的智能平台
针对碳纤维-环氧树脂、碳纤维-热塑性塑料等不同基体材料,Dolphicam2支持参数自定义配置,确保检测方案与材料特性高度匹配。此外,其便携式设计可无缝适配实验室与生产线场景。
数据驱动的寿命预测
通过整合历史检测数据与力学性能模型,Dolphicam2能够预测缺陷演化趋势,为构件的维修决策提供科学依据。这一功能在风电叶片、高铁车体等长周期服役场景中价值显著。
四、行业应用与未来展望
在新能源汽车领域,Dolphicam2已助力多家企业实现电池箱体碳纤维外壳的零缺陷交付;在航天领域,其被用于火箭燃料储罐的在线检测,将质检周期缩短60%。随着碳纤维在氢能储罐、超导磁体等新兴场景的应用拓展,高灵敏度、智能化的无损检测技术将成为产业升级的核心驱动力。
青岛纵横仪器有限公司:复合材料检测领域的
作为国内的无损检测设备供应商,青岛纵横仪器有限公司深耕复合材料领域十余年,其自主研发的Dolphicam2系列产品已服务覆盖航空航天、轨道交通、能源装备等市场。公司凭借定制化解决方案、快速响应能力与全天候技术支撑,成为行业客户的合作伙伴。
如需了解更多Dolphicam2的技术细节或获取免费样机演示,请联系纵横仪器销售团队:135-0542-5410,我们将为您的材料可靠性保驾护航。
继续阅读与本文相关的标签