复合材料缺陷检测难题如何破局?Dolphicam 2智能探伤系统带来革新方案
所在栏目:行业快讯
发布时间:2025-04-29 15:07:07
关注度:9
当一架飞机因复合材料层压板出现分层缺陷而停飞检修,或是一台风力涡轮机叶片因内部孔隙超标导致断裂事故时,工程师们总会面临同一个核心问题:如何在材料失效前精准定位缺陷? 随着复合材料在航空航天、新能源、轨道交通等领域的广泛应用,其内部缺陷的检测需求正呈现指数级增长。从毫米级的孔隙到隐蔽的分层裂纹,这些“隐形杀手”的检测效率与精度,直接关系到工业设备的安全性与使用寿命。
一、复合材料缺陷的“潜伏危机”:类型与危害
复合材料因其轻量化、高强度特性备受青睐,但复杂的制造工艺与环境载荷使其易产生三类典型缺陷:
制造缺陷:包括树脂分布不均、*纤维褶皱*和孔隙聚集,这类缺陷多源于成型工艺参数偏差
结构损伤:如分层、*脱粘*和冲击损伤,常由外部机械应力或热应力引发
服役缺陷:*疲劳裂纹*和腐蚀侵蚀,随时间推移逐渐恶化结构完整性
据国际航空安全协会统计,超过60%的复合材料部件失效案例源于未被及时发现的亚表面缺陷。传统目视检测和敲击法仅能识别表面损伤,而X射线、超声波等常规手段又面临检测效率低、操作复杂等瓶颈。
二、传统检测技术的“力不从心”
当前主流检测方法存在三大痛点:
灵敏度局限:常规超声检测对0.5mm以下孔隙的漏检率高达35%
效率瓶颈:大型风电叶片全尺寸检测需耗时8小时以上
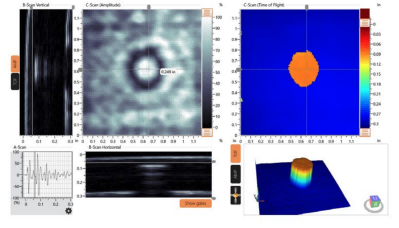
数据断层:二维成像无法直观呈现缺陷三维特征
某轨道交通企业曾因采用传统红外热成像技术,导致车体碳纤维加强梁的微裂纹漏检,最终引发批量返工事件。这类案例凸显了行业对高精度、高效率、智能化检测方案的迫切需求。
三、Dolphicam 2:重新定义复合材料无损检测标准
青岛纵横仪器有限公司研发的Dolphicam 2智能探伤系统,通过三大技术创新突破行业痛点:
1. 多模态融合检测技术
集成*相控阵超声(PAUT)*与*激光散斑干涉*技术,实现从表面到内部的全维度扫描
0.1mm分辨率精准识别分层、孔隙等缺陷,检测精度较传统设备提升300%
2. AI驱动的智能诊断系统
搭载深度学习算法库,可自动分类17种缺陷类型并评估风险等级
实时生成三维可视化报告,缺陷定位误差小于±0.3mm
3. 革命性操作体验设计
单手操控的轻量化探头(仅1.2kg),适应曲率半径≥50mm的复杂曲面
配备*IP67防护等级*与-20℃~60℃宽温域工作能力,满足野外作业需求
在2023年某航天复合材料舱体检测项目中,Dolphicam 2仅用传统方法1/4的时间即完成全舱扫描,成功识别出3处被漏检的微米级分层缺陷。
四、为什么选择青岛纵横仪器?
作为国内少数掌握复合材料全流程检测技术的高新技术企业,青岛纵横仪器拥有:
12项优势覆盖超声相控阵、激光散斑等核心领域
实验室提供检测设备校准与工艺验证服务
200+行业解决方案应用于风电叶片、储氢罐、飞机蒙皮等场景
即刻致电135-0542-5410获取Dolphicam 2技术白皮书与定制化检测方案。我们的工程师团队可提供现场演示、*对比测试*及*技术培训*全流程服务,助力企业构建复合材料质量控制新范式。
注:系统参数基于青岛纵横仪器内部测试数据,实际性能可能因检测环境与材料特性存在差异。
继续阅读与本文相关的标签